Technical parameter
Device model |
VLT-1000B |
VLT-1200B |
VLT-1400B |
VLT-1500B |
VLT-1600B |
VLT-1800B |
VLT-2000B |
Size |
1000×1500 |
1200×1650 |
1400×1800 |
1500×1850 |
1600×1950 |
1800×1950 |
2000×2100 |
Type of film: auto lamp reflective aluminum film automatically completes the coating and protective film overlap process at one time
Power supply type: double door, air extraction system
Vacuum system: slide valve pump + roots pump + diffusion pump + maintenance pump (or optional: cryogenic pump, cryogenic system)
Protective film monomer: independent stainless steel gas tank
Inflation system: mass flow controller control
High pressure bombardment system: 13KVA 3000v
Ultimate vacuum: 6×10-4pa (no load, clean room)
Pumping time: no-load air pumping to 5×10-2pa less than or equal to 6 minutes
Workpiece rotation: single axis/6 axis/8 axis revolution and rotation/dual frequency stepless speed regulation
Control method: manual + semi-automatic + fully automatic integration / touch screen + PLC
Remarks: The size of the vacuum chamber can be customized according to customer's product and special process requirements
Equipment characteristics
The same period of production: -900sec/(15 minutes) shorter than the same period of production for similar equipment
Coating method: heating system evaporation coating and protective coating are completed at the same time (no other anti-gasification treatment is required after coating)
Coating quality: Each door has 6-8 sets of fixtures for both rotation and revolution. The coating thickness is uniform, which is suitable for mass production of economical car lights.
Dehumidification capacity: the vacuum chamber is equipped with an ultra-low temperature refrigeration system below minus 140 degrees, which fully absorbs moisture to increase the vacuum reach speed
Operating cost: The volume of the vacuum chamber is relatively large, the number of coatings is large each time, and the operating cost of a single piece is low
Number of fixtures: According to the size of the product, the fixture can be changed to 6 axis or 8 axis at will, without any installation and adjustment when changing
Defective product rate: omit the usual processing procedures (primer coating and aluminum film protective paint spraying) to reduce defective products
Floor area: double-door structure, relatively smaller installation area and operation area than similar equipment
Operation method: The man-machine interface can be set and monitored intuitively, and the person who has no management password can not change it
After-sales service: There is an after-sales service center and parts warehouse, which can quickly deal with problems in use
Equipment principle
In a suitable vacuum environment, the heating wire is supplied with a certain voltage, so that the aluminum wire placed on the heating wire evaporates on the surface of the rotating product to achieve the purpose of aluminum plating. The HMDSD (paint) and Nitrous (N20)
Under the high voltage of several hundred volts, it reacts into silicon gel (Si02), and adheres to the metal film plated in the previous process to prevent oxidation.
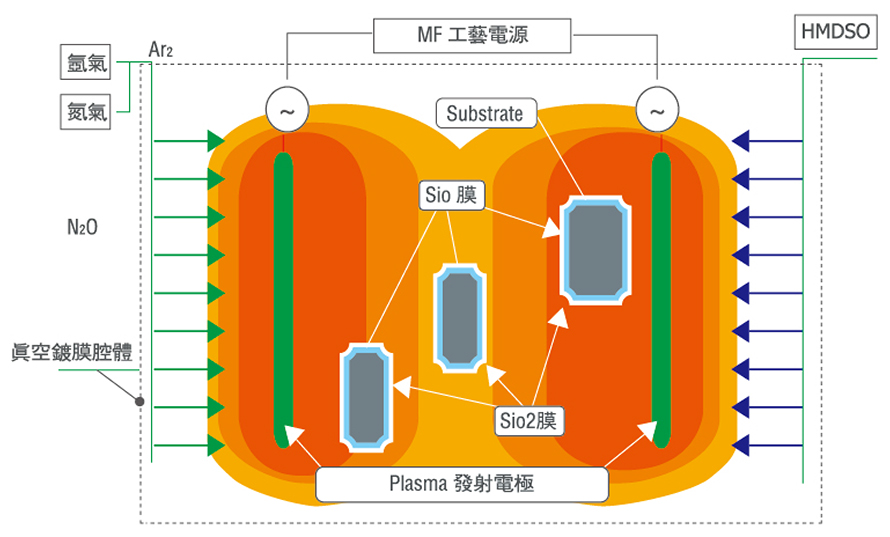
Schematic diagram of protective coating
Clean the surface of the injection molded object by generating an electric arc at an intermediate frequency
Activation to improve the adhesion of coated articles
Fully exhaust in a high vacuum environment
Metal coating through DC power supply
Protective film coating through intermediate frequency power supply
Carry out the hardening of the protective film
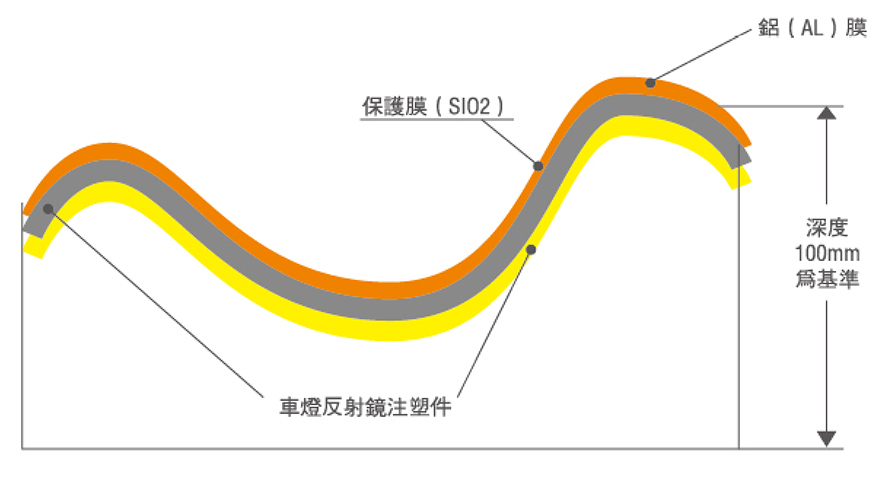
產品鍍膜原理圖